In the pharmaceutical Active Pharmaceutical Ingredient (API) manufacturing sector, process safety is critical due to the hazardous chemicals and complex processes involved. Our client, a leading pharmaceutical API manufacturer, recognized the need to adopt a Risk-Based Process Safety Management (RBPSM) system to mitigate process-related risks and enhance operational safety.
This case study outlines the detailed, phase-wise approach used to implement RBPSM across their facilities, covering risk identification, strategy framing, training, real-time monitoring, and data-driven decision-making. This case study outlines the structured approach taken to implement RBPSM over 3 years. It provides a detailed account of each phase, highlights the data-driven decisions made, and showcases the impact of the project using statistical insights.
Client Industry
Pharmaceutical API Manufacturing
Project Duration
3 Years
Consultant Involved
4 (Total Consultant)
BBS Consulting Project Phases and Approach
Phase 1 - Gap Assessment (First 4 months)
The RBPSM implementation began with a thorough gap analysis to identify current process safety shortcomings:
- Process Audits : Conducted extensive process safety audits across the API production plants.
- Risk Assessments : Identified potential hazards using risk assessment techniques like HAZOP (Hazard and Operability Study) and LOPA (Layer of Protection Analysis).
- Incident Data Review : Analyzed past safety incidents and deviations in the manufacturing process.
- Employee Interviews : Engaged with operators, engineers, and supervisors to understand safety awareness levels.
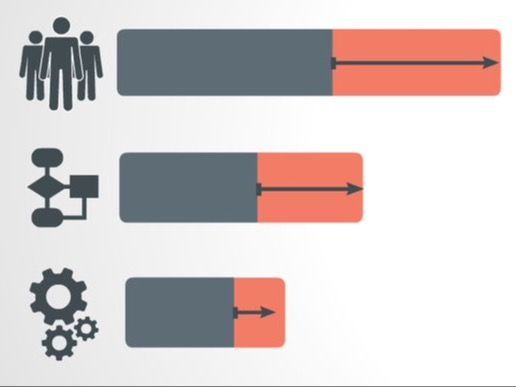
Phase 1 - Key Findings
Safety Control
Several critical equipment and processes were operating without safety controls
Data Analytics
Limited use of advanced data analytics for risk prediction and incident prevention.
Risk Based Thinking
Gaps in employee understanding of process risk management.
Statistical Highlight: Phase 1
60% of past incidents were attributed to failures in the risk control system.
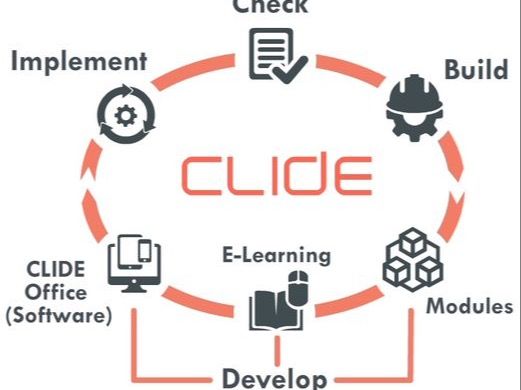
Phase 2 - Framing the Strategy (Months 5-9)
Based on the gap assessment, we developed a tailored RBPSM strategy with a focus on mitigating high-priority risks in API manufacturing:
- Leadership Engagement: Ensured buy-in from top management for long-term success.
- Development of RBPSM Policies: Drafted company-wide safety policies and practices.
- Hazard Identification and Control: Prioritized areas such as reactor operations, solvent handling, and material transfers for immediate intervention.
Data Driven Decision : Phase 2
The initial focus was placed on areas with high process deviation rates, such as the synthesis section, where 70% of potential hazards were identified.
Phase 3 - Training & Skill Development (Months 10-17)
Effective implementation of RBPSM required intensive training and capacity building across the organization:
- Specialized Training Programs: Over 500 employees were trained in risk identification and process safety management, including senior management, engineers, and operators.
- Workshops and Simulations: Hands-on workshops were conducted, focusing on real-life case studies and emergency drills.
- Safety Leadership Programs: Leadership workshops to empower department heads with safety oversight skills.
Enhanced cross-functional safety collaboration across production, engineering, and quality assurance teams.
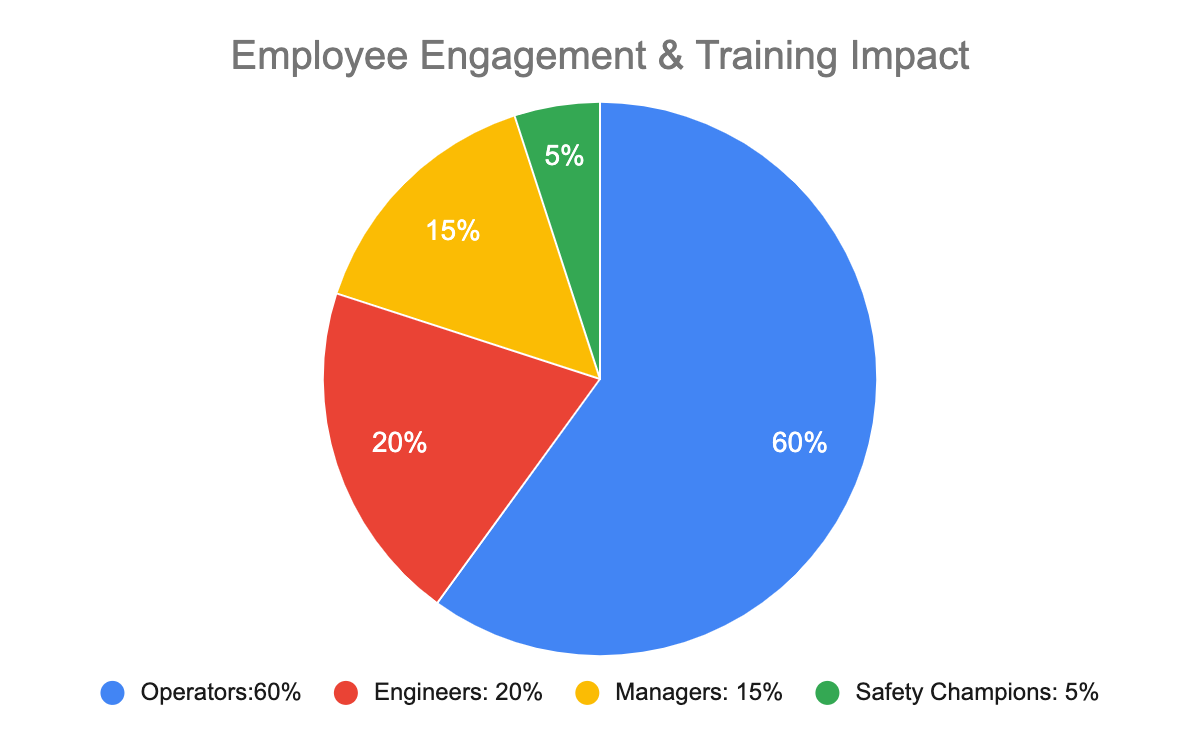
Phase 3 - Key Results
RBPSM Training
Over 2,000 employees were trained in RBPSM Elements.
Reporting
40% increase in the number of safety issues proactively reported by employees.
Employee Engagement
63% participation increase in safety activities by frontline workers
Statistical Highlight: Phase 3
85% of employees expressed improved confidence in identifying and managing process risks after the training.
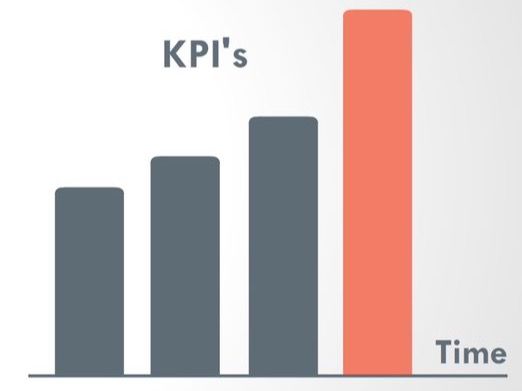
Phase 4 - Handholding & Implementation Support (Months 14-27)
This phase involved on-site support to ensure smooth execution of the RBPSM framework:
- Continuous Consultant Support: Our team of four consultants remained embedded in key departments to guide implementation and address challenges.
- Real-Time Monitoring: A new digital safety monitoring system was introduced to capture real-time data on equipment conditions, deviations, and alarms.
- Process Hazard Analysis (PHA) Reviews: Conducted reviews of critical systems with enhanced hazard identification tools to strengthen preventive measures.
Phase 4 - Impact
Reporting
Over 25,000 process safety observations logged.
Risk Reduction
60% reduction in operational risks and near misses in high-priority areas.
Incident Rate
Saw 33 % reduction is incident rate across all the location due to risk failure.
Data Driven Decision : Phase 4
Real-time monitoring revealed frequent deviations in temperature controls during solvent reactions. This insight led to changes in reactor operating procedures, reducing the likelihood of thermal runaway incidents.
Phase 5 - Review Meetings & Continuous Improvement (Months 23-36)
Regular review meetings were conducted to evaluate the effectiveness of the RBPSM system and ensure continuous improvement:
- Monthly Safety Reviews: Discussed key safety performance metrics, incident data, and behavioral observations.
- Root Cause Analysis: Conducted in-depth reviews of any safety incidents or near misses to refine safety protocols.
- Feedback Loops: Continuous feedback was sought from employees to improve risk control measures.
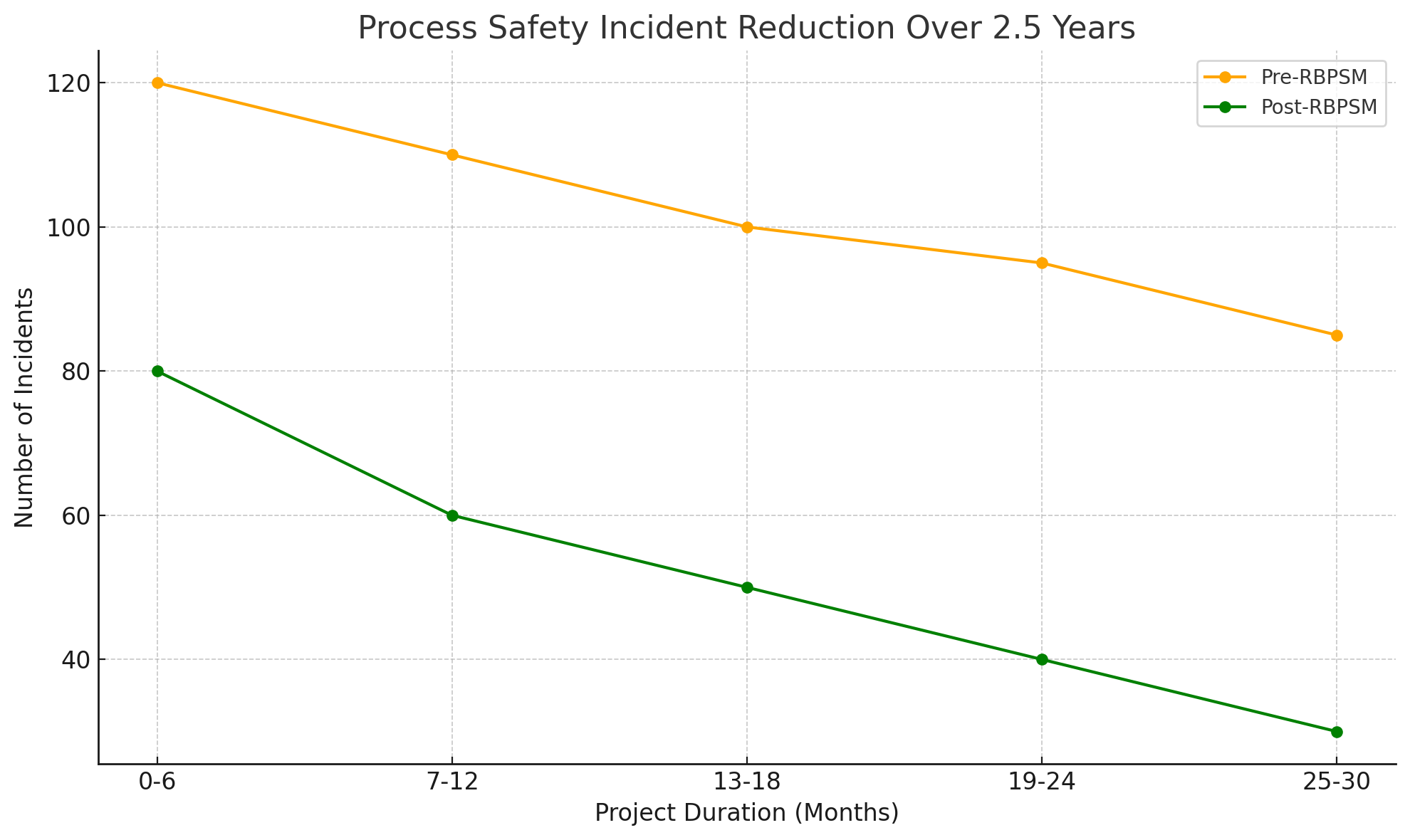
Phase 5 - Key Impact
Incident Rate
Achieved a 50% reduction in process safety-related incidents.
Compliance Rate
Improved safety audit scores by 74% across all API manufacturing units.
Process Safety Culture
73% Increase in safe behaviour at the workplace across all location
Statistical Highlight: Phase 5
100% compliance with newly implemented risk controls, resulting in zero major incidents in the last 12 months of the project.
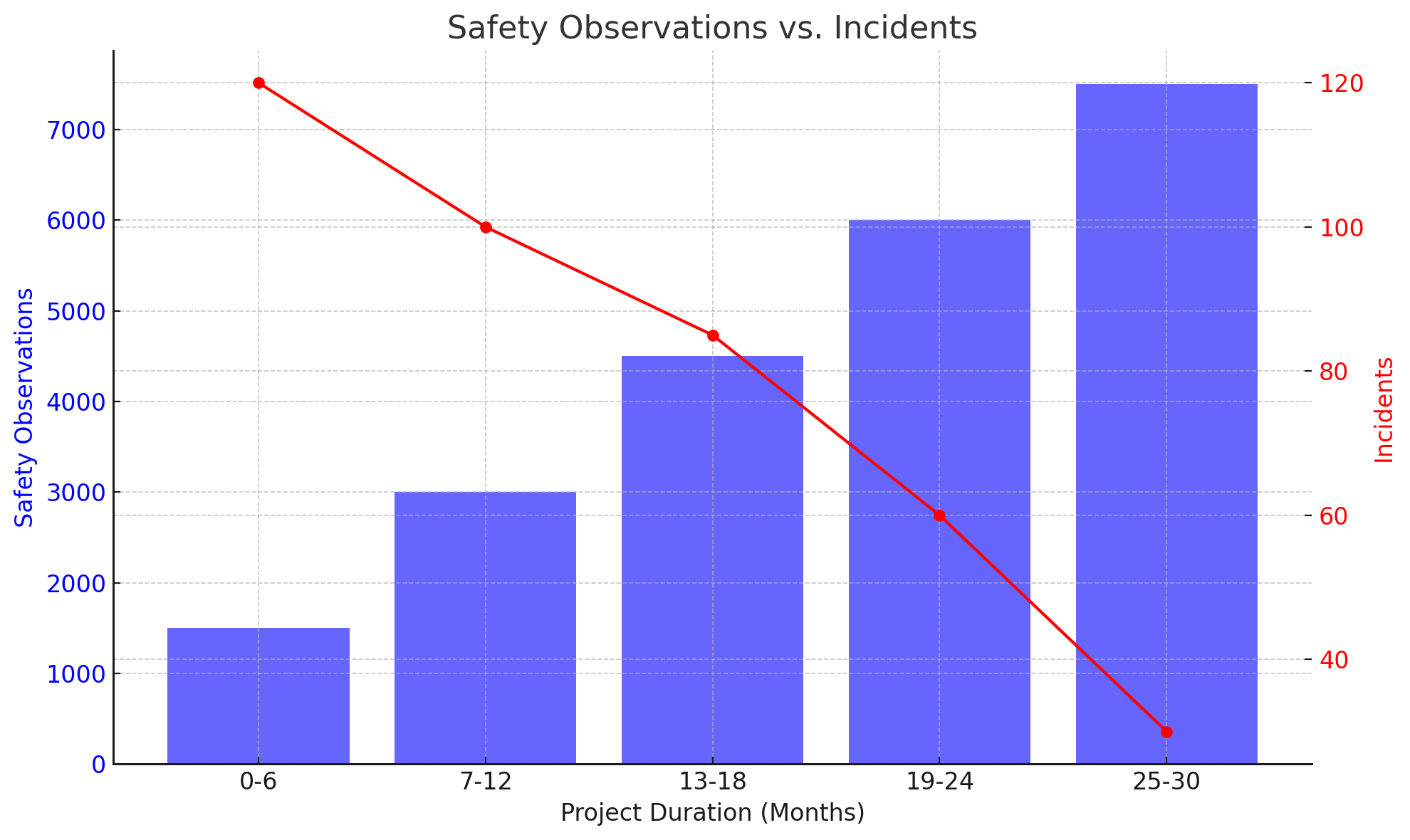
Phase 6 - Data Analytics & Tools (Ongoing)
A critical success factor for this RBPSM project was the integration of data analytics tools for predictive risk management:
- Custom Dashboards: Real-time safety dashboards were deployed to track risk factors, equipment conditions, and operational data.
- Predictive Analytics: The system used historical data to predict high-risk periods, enabling proactive interventions before incidents occurred.
- Key Performance Indicators (KPIs): Monitored KPIs such as deviations per shift, risk assessment closures, and safety audit compliance.
Data Driven Decision : Phase 6
Based on predictive analytics, the company introduced new control systems for their solvent distillation process, reducing the risk of fire or explosion by 35%.
RBPSM Consulting Project Outcome & Results
The implementation of Risk-Based Process Safety Management (RBPSM) transformed the client's approach to operational safety, resulting in significant improvements. Below are the key metrics that demonstrate the success of the project:
Safety Incident Reduction
50% drop in incidents related to process failures and risk control breaches.
Real-Time Risk Monitoring
Over 25,000 safety observations logged using the digital tool.
Employee Engagement
40% increase in proactive reporting of process deviations and near misses.
The successful implementation of the Risk-Based Process Safety Management (RBPSM) system in the pharmaceutical API industry resulted in significant reductions in process-related risks, improved employee safety awareness, and the establishment of a proactive safety culture. The use of data analytics and real-time monitoring tools enabled better decision-making and helped sustain these improvements long-term.