How to develop process safety KPIs to drive safety performance Improvement?
What KPIs are you using to measure process safety improvement?
Process Safety KPIs are measurable values used by Health and Safety Teams to track and determine their progress on specific business objectives. These KPIs help determine how well H&S Teams are performing. Indeed, plenty of organisations won't have even considered creating KPIs but instead used standard KPIs as available in open source.
Many companies have a KPI-driven culture, therefore, caution is needed in determining the right indicators and targets for companies with this type of culture as the individuals may see their role as managing the indicator rather than managing the process that it is indicative of.
The development of the Process Safety KPIs for our client was undertaken in four stages, this KPI development activity was part of a much larger assessment of how the company managed process safety at the time.
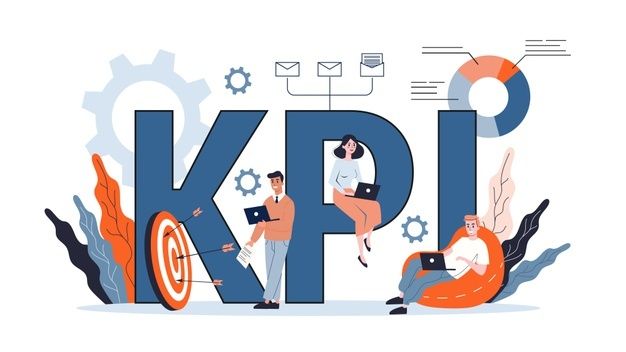
Stage 1 - Current Process Safety KPIs Review
Reviewing the performance mechanisms and indicators that the company already had in place.
Stage 2 - Develop New Sets of Comprehensive Process Safety KPIs
Develop a comprehensive list of Process Safety KPIs based on good practice & considered for use within the company.
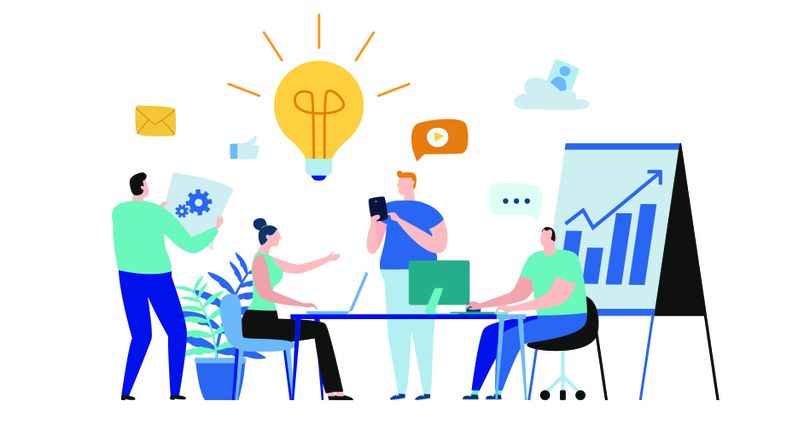
STAGE 3: Priorities KPIs Set as per Business Process Need
The KPIs where priorities into three categories to drive performance improvement.
- Category One – required immediate attention
- Category Two – requiring attention in the medium term
- Category Three – requiring attention in the longer term.
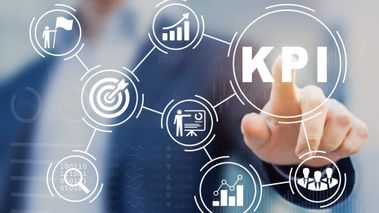
Stage 4 - Develop Final Process Safety KPIs to monitor safety improvement.
Strong action plan to implement the developed KPIs and its buy-in from all the stakeholder for improvement.
RACI
Also included RACI chart for the KPIs. The RACI chart describes the positions in the company who are Responsible, Accountable, Consulted and Informed about each KPI, and therefore sets out the reporting hierarchy for the KPIs
KPI Data Visualisation Format
- Traffic Light
- Heat Maps
- Progress Graphs
It is the ‘acting upon’ that is crucial to the improvement in PSM performance. Measuring alone will not drive this improvement. The information the KPIs provide must be used by senior managers to change PSM policy, procedures, practices and beliefs, and it is these changes that will drive PSM improvement, one word “Leadership”.